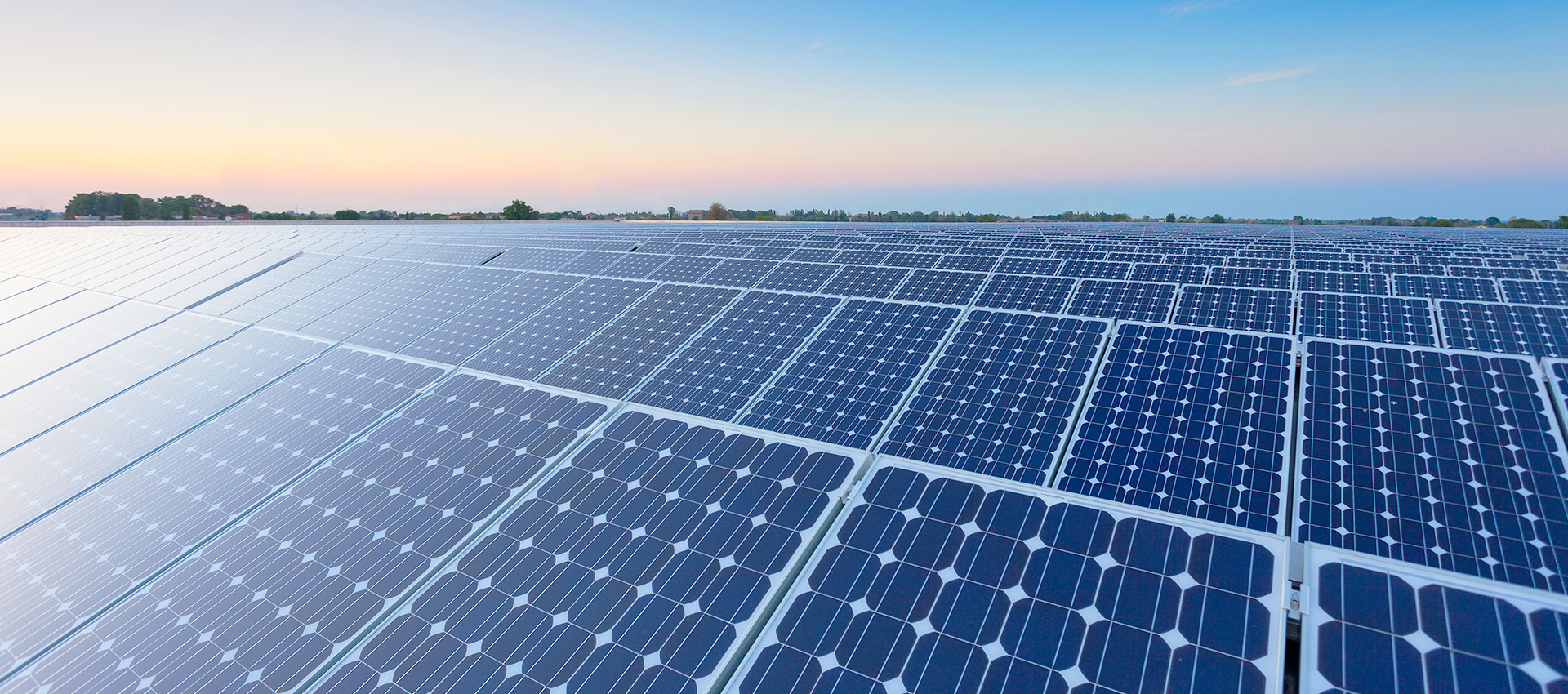
Ground Mounting of Photovoltaic Racking
2023-12-21Solar Mounting Structure Panel Ground Mount System
Photovoltaic bracket has angle-fixed steel structure bracket, automatic tracking bracket and aluminum alloy bracket, etc. Among them, aluminum alloy bracket is generally used in small-scale roof photovoltaic power generation system and large-scale steel structure bracket to fix part of the battery component bracket, with corrosion resistance, light weight, beautiful and durable features, but low bearing capacity and high price; automatic tracking bracket due to the cost, efficiency and so on, the application is not yet common; Steel structure bracket has stable performance, mature manufacturing process, high bearing capacity and easy installation, which can be widely used in various types of photovoltaic power stations.
PV bracket can be divided into welding and assembling two kinds according to different connection methods. Welded bracket on the steel section (channel steel and angle steel) production process requirements are low, the connection strength is better, the price is low, but the welded bracket also has some shortcomings, such as the connection point of the anticorrosion difficulty. If paint is applied, the paint layer will flake off every 1 to 2 years, which needs to be repainted and the subsequent maintenance cost is high. Welded brackets are generally made of hot-dip galvanized steel or ordinary angle steel, and corrosion-resistant steel such as stainless steel can be considered for coastal areas. The average thickness of galvanized layer of hot-dip galvanized steel should be more than 50 μm, and the minimum thickness should be more than 45 μm. The welding quality of the bracket should meet the requirements of the national standard “Code for Acceptance of Construction Quality of Steel Structural Engineering” (GB 50205-2001). All of the ordinary steel brackets and the welded parts of hot-dip galvanized steel brackets should be coated with antirust paint and other anticorrosion treatment.
The assembled bracket takes the finished steel section or aluminum alloy as the main supporting structural parts, which has the advantages of easy assembling and disassembling, no need for welding, even anticorrosion coating, good durability, fast construction, beautiful appearance, etc., and it is the commonly adopted bracket connection method at present. The installation sequence of PV bracket is as follows.
(1) Installation of front and rear columns, columns should be perpendicular to the foundation, screw on the pre-embedded nut, eat the strength can be, do not tighten first. If there is a channel steel bottom frame, the first channel steel bottom frame and the foundation leveling fixed or welded firmly, and then the front and rear columns fixed in the channel steel bottom frame on the corresponding position.
(2) Installation of column connecting rod. When installing the column connecting rod, the surface of the connecting rod should be placed on the outside of the column and the fixing bolts should be tightened to 6 minutes.
(3) Install the front and rear crossbeams. Place the front and rear crossbeams on the steel pillars and fix them with the steel pillars, level and straighten the crossbeams with a level meter, tighten the bolts again, check the front and rear beams again with a level meter, and tighten the bolts thoroughly after there is no problem.
Although there are differences in the structure and connectors of different types of stents, the installation sequence is basically the same, and the specific installation methods can refer to the design drawings or technical information provided by the stent manufacturers.
PV bracket and the foundation should be welded or mounted firmly between the bottom surface of the column and the concrete foundation contact surface with cement slurry to add irrigation, so that it is tightly combined. The bracket and PV module frame should be reliably connected to the protective grounding system.